祖業のプレス加工・ブレージング(ろう付け)加工に加え、2014年から自社開発のデータロガー(記録計)を販売。2019年、新社屋・工場を設立。
Q. DX推進に至ったきっかけは。
-中西社長 もともと自社製品を開発したいと思っていたところ、2010年頃、センサーに詳しい技術者と出会い、社内ベンチャーを立ち上げました。そこで試行錯誤しているうちに、ある大学から「ビニールハウス内のトマトの生育状況を見るために、温度・湿度・照度のデータが取れるデータロガーを作ってほしい」と依頼されたんです。開発はうまく進み、納品したデータロガーは先方に満足していただきました。それを製品化し、2014年から「ログビー」という名前で農業向けに外販し始めたんです。ところが、ログビーは3年間全然売れませんでした。
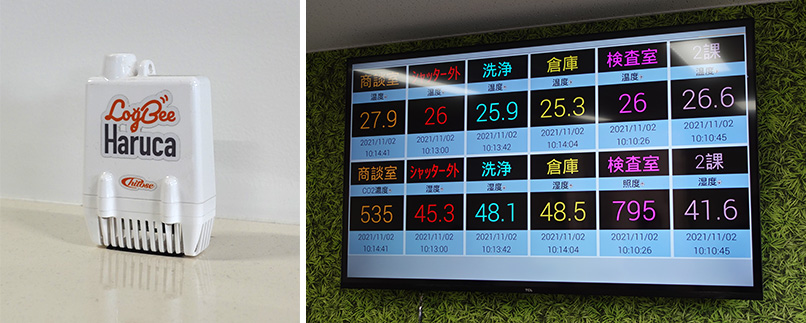
社内各所に配置された「ログビー」と、それにより可視化された社内環境
Q. その後、どのように販路を獲得したのでしょう。
-中西社長 デジタルマーケティングに力を注いだところ、建設業界のニーズが高いことが分かりました。コンクリート養生の際の湿度管理に役立つことで、国土交通省の「NETIS(新技術提供システム)」に登録されました。その後、食品・農業・医療の分野でも使ってもらえるように。ユニークな例では、「海外輸出時に検査工程のトレーサビリティーに必要」という中古車業者からの依頼もありましたね。
Q. 経営内容や社内・社員に変化はありましたか。
-中西室長 2019年に新工場を設立しました。ログビーは以前の工場の時から取り入れていますが、金属の変色を防ぐための湿度管理、加熱炉の近くで作業するブレージング加工場のための熱中症指数測定、検査室の照度測定など、製品の品質保持や作業環境の管理に役立っています。CO2濃度のセンサーを搭載したログビーもあり、事務所や会議室などは換気状況を可視化できています。コロナ禍においては特に、事務所で勤務する社員や来社されるお客様の安心感につながりました。
また新工場はスマートファクトリーのモデル工場でもあります。プレス加工の部署ではショットセンサー(加工数量カウンター)を導入し、生産性の可視化を図りました。リアルタイムで稼働状況を把握できるので、社員の意識が高まり、スピード感を持って仕事をするようになったと思います。
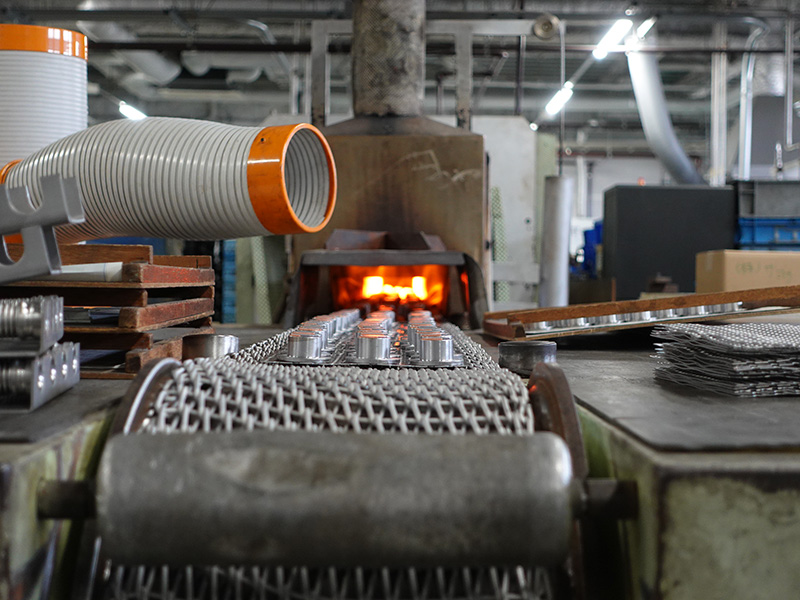
加熱炉が印象的なブレージング加工場
Q. 今後どのような展開を検討されていますか。
-中西社長 ログビーの開発部署である事業開発部の構想としては、現在の「生産性の見える工場」から、予防管理ができる「止まらない工場」へ、さらにサプライチェーンの連携などを考えた「つながる工場」へ。その3ステップを実現させたいと考えています。
-中西室長 新工場で導入した「生産性の可視化」システムの外販もめざしています。まだ当社で実験を重ねている段階ですが、強みとしてはそもそも当社が加工メーカーであり、社内で開発・フィードバックができるということ。システム外販の際は、リーズナブルに提供できると思うので、スモールスタートを考えている企業に購入いただけるのではないかと考えています。